The increasing need for lightweight design, combined with improved functionality, quality and economic build, continues to drive the need for comprehensive testing within key structural systems and components in the Aerospace sector.
The complex stresses that occur during the operation of technical structures must be examined under static and dynamic operational loads to assess the impact of fatigue and also to determine accurate in-service life predictions. Element has multiple hydraulic cylinders and high capacity measuring systems that can handle more than 250 channels.
These systems are available to test complex assemblies and components under multiple multiaxial stress scenarios. We can also test these components at temperatures from -70°C up to 415°C as well as under extreme loads or special climactic conditions (e.g. moisture and temperature).
With a large suite of structures testing inventory comprising of more than 60 actuators and load cells covering a range of 1kN to 1MN, two configurable multichannel control as well as appropriate expandable data acquisition systems, Element has demonstrated the capability and the know-how to perform most complex and highly sophisticated test campaigns over the last decades. The following examples provide a good insight into this special type of testing.
Ready to request a quote?
Our deliverable is certainty - high quality data, test reports and certificates that you can absolutely rely on when making decisions about your materials and compliance. Engage with an expert today.
More details
Other Product Qualification Testing Services
Accelerated Aging
Accelerated Weathering Testing
Acceleration Testing
Aircraft Ditching Testing
Altitude Testing and Simulation
Bird Strike Testing
Breath Alcohol Ignition Interlock Device
Component High Cycle Fatigue Testing
Dynamics Testing
Advisory Services
Electromagnetic Compatibility (EMC) Testing
Electronics Test Methods
Environmental Testing
Explosive Atmosphere Testing and Certification
Flame Fire and Flammability Testing
Flame Resistance and Fire Proof Testing
Fluid Susceptibility Testing
Fuel System Testing
Hail Impact Testing
HALT Testing and HASS Testing
High Cycle Fatigue Testing
High Level Acoustic Noise Testing
Highly Accelerated Stress Testing
Hose Testing
Humidity Testing
Hybrid and Electric Vehicle Battery Testing
Ingress Protection Testing
International Certifications and Approvals
Liquids and Fuels Testing
Low Lubricity Aircraft Fuel Testing
MIL-STD-810 Testing
Pneumatics Testing
Pressure Testing
Product Certification Services
Product Compliance Services
Product Safety Testing
RTCA DO-160 Testing
Salt Fog and Salt Spray Testing
Sand and Dust Testing
Seismic Testing
Shock Testing
Space Simulation
Spin Testing
Structures Testing
Temperature and Thermal Testing
Thermal Vacuum Testing
Towing Trailer and Hitch Product Testing
Vibration Testing
VOC and SVOC Testing
Wireless Radio Testing
Zigbee Certification Services
aerospace structures testing
More from Element
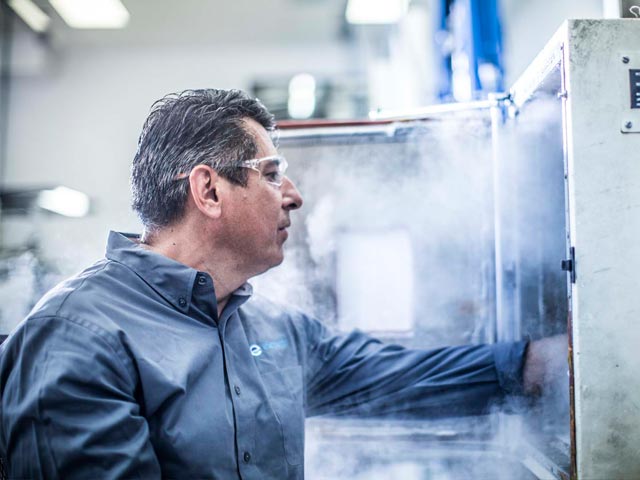
services
Product Testing
From environmental and dynamic testing to highly specialized tests such as bird strike and hydrodynamic ditching testing, we're the trusted testing partner to the world's most recognized component and system manufacturers.
Read More
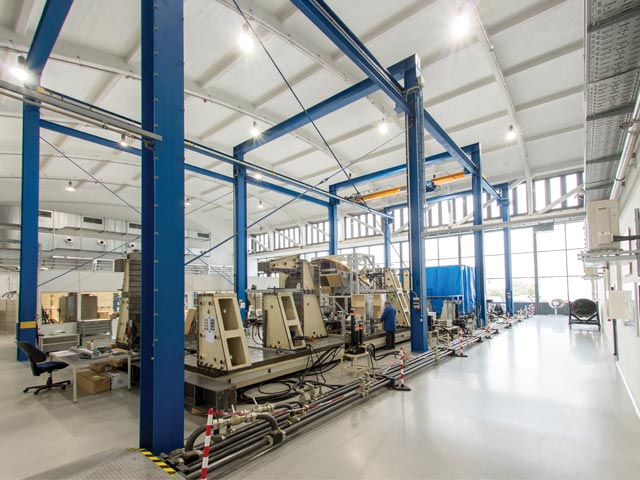
Center of Technical Excellence
元素Berlin
元素Berlin is a leading Aerospace laboratory specializing in complex product testing services requiring large scale rigs and equipment such as spin testing, structures testing and fluid dynamics testing.
Read more
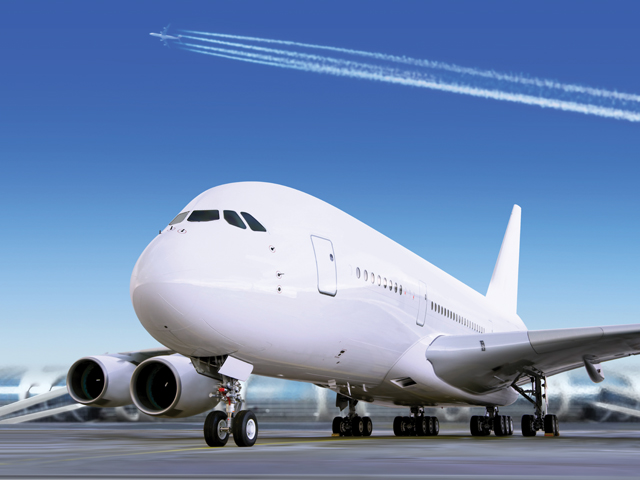
aerospace
Our Services in Aerospace
Engaged in testing virtually every material, component and system on commercial aircraft, Element's deliverable is mission critical, certainty.
Read more
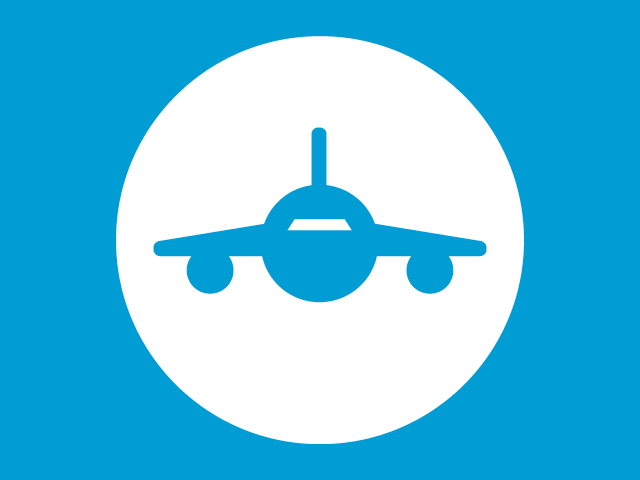
news
Element Acquires TRaC GLobal
Element’s continued investment in its Aerospace Product Qualification Testing (PQT) ensures that it remains uniquely positioned to deliver on both the PQT and Materials Testing requirements of Primes and their supply chain partners.
Read full article
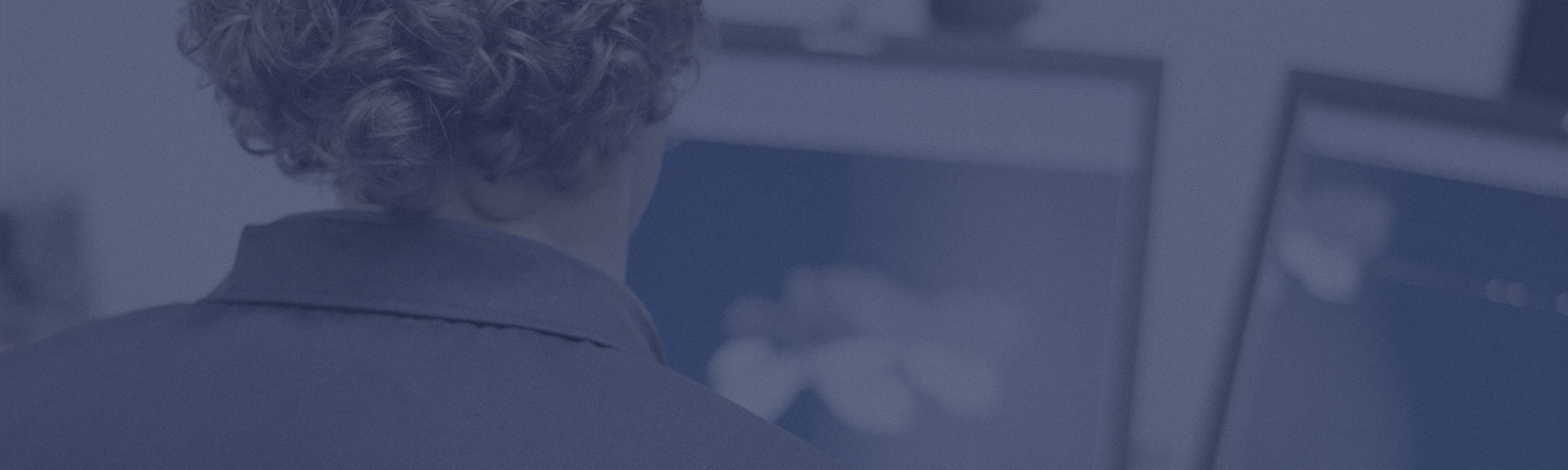