Composite sandwich panels are made of two thin, stiff face sheets bonded to a relatively thick, lightweight core. To understand the durability and performance of a sandwich panel, the entire construct must be tested together.
Composite sandwich materials have stiff skin around the core which provides superior bending properties with lower weight. The constructs are commonly used in aircraft, satellites, marine and automotive applications, and wind turbines. Element provides a variety of mechanical testing methods to evaluate the properties of composite sandwich structures, including flatwise tensile, core and plate shear, bending, and compression.
Composite sandwich panel test methods
Our experts performout-of-plane or flatwise tensileaccording to ASTM C297. The test set up requires bonding the skins to loading blocks and pulling them apart perpendicular to the sandwich panel. The failure mode typically takes place in the core and sometimes in the adhesive.
Core shear or plate shear testingis a useful method for understanding theshear propertiesof the sandwich construct. When testing according to ASTM C273, the sample skins are bonded to the plates and loaded in opposite directions in the plane of the sandwich panel, creating a shear condition. The failure mode typically takes place in the core. In-plane shear may also be performed using a “picture frame” configuration. Element provides panel shear testing for specimens of various sizes and to high loads.
ASTM C393 outlines the process forbend testing三明治的材料。yabo娱乐vip不同的属性可能是我asured by changing the span of loading. For example, a shorter span of loading provides data for core shear properties and a longer span of loading provides data for skin properties.
元素执行compression testingboth in-plane and out-of-plane. ASTM C364 provides guidance for in-plane or edgewise compression testing, and ASTM C365 covers out-of-plane or flatwise compression testing. Both compression methods help determine modulus data.
To simulate in-service damage, composite sandwich panels undergofatigue testingin either bend or compression to evaluate damage growth. In these cases, the materials may have impact damage, or flaw deliberately included during construction.
Adhesive bond testing
The adhesive bond used to connect the sandwich panel materials is evaluated in peel. Climbing drum peel, outlined in ASTM D1781, is a common quality control test for sandwich panel construction. Element is involved in the development of current methods for more analytical cantilever peel methods.
Composite testing at Element
Ourcomposite testingexperts have a breadth of experience testing composite sandwich panels to a variety of test methods and specifications. We work diligently to ensure your materials and constructs are quality, compliant, and fit-for-purpose.
For more information about testing sandwich panel constructs or to request a quote,contact us today.
making certain for nearly 190 years
更多来自元素
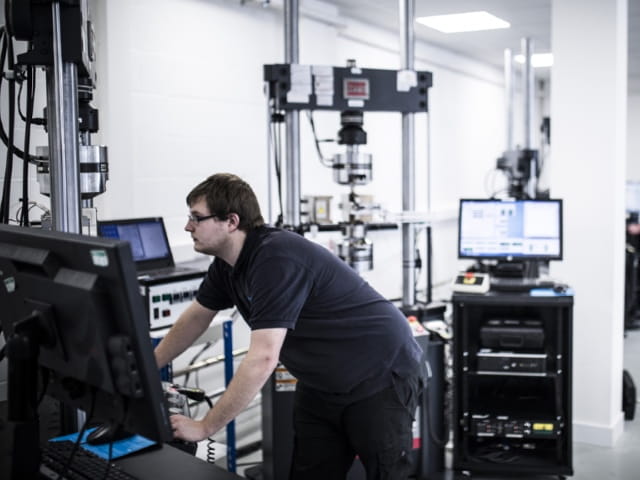
Composite Fatigue Testing
Whether testing to a specific standard or developing a custom program, Element’s experts are ready to assist with your composite fatigue testing needs.
Read More
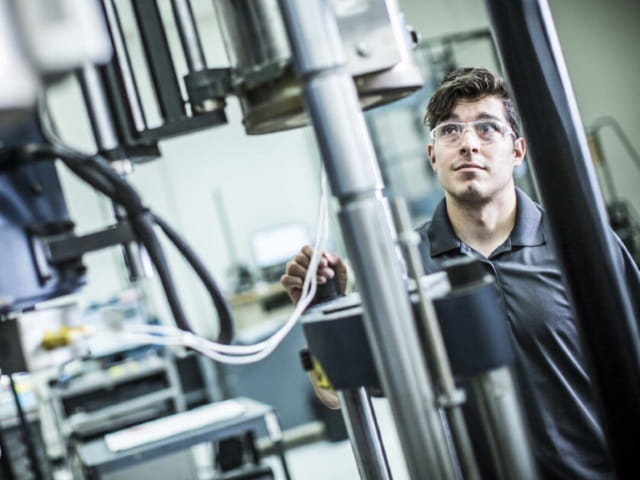
Shear Testing of Composites
Our composite testing experts provide shear testing methods including interlaminar, in-plane, and v-notch to measure the shear properties of your material.
Read More
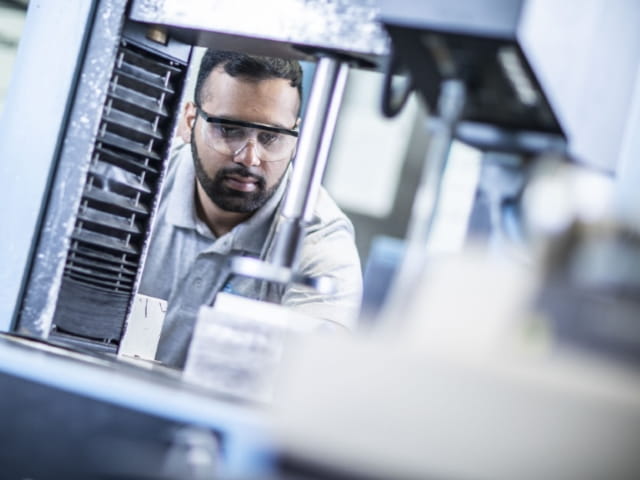
Understanding Composite Compression Test Methods
While there is no set standard for testing the compressive strength of composites, our experts can help you select the test methods that will generate the required result.
Read More
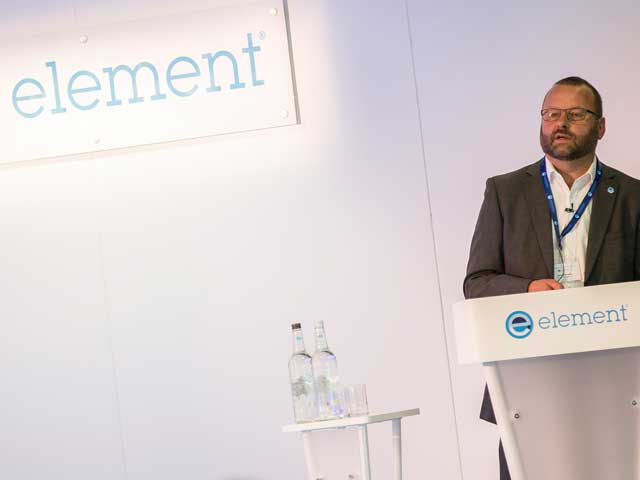
亚慱体育怎么下载
Discover blog posts, articles, white papers, webinars, and advice from our world-leading testing, inspection, and certification experts.
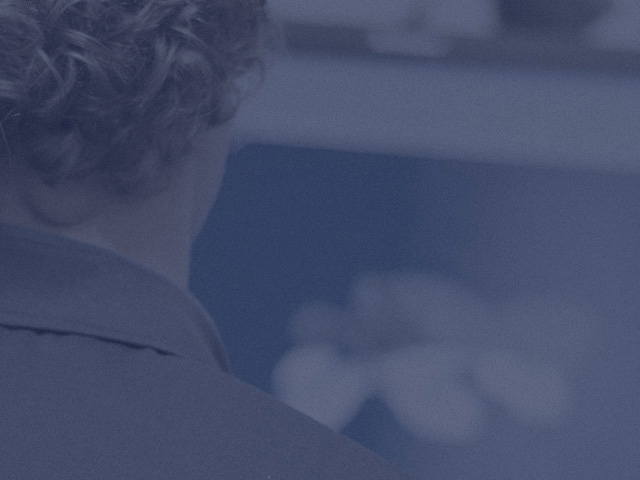