Element’s Fitness for Service (FFS) assessments help determine if your equipment is safe and fit for continued operation. It prevents failures, minimizes risks, and eliminates costly repairs.
Assessment procedures are used by the Oil & Gas, Power Generation, and Chemical Processing industries forintegrity managementand to evaluate fitness for service of pressure containing equipment.
Element can evaluate the structural and mechanical integrity of a wide range of components to API 579-1/ASME FFS-1 international standards, including boiler, HRSG, pressure vessels, chemical reactors, storage tanks, piping systems, and pipelines. From design to decommissioning, our Fitness for Service assessments help you avoid brittle and ductile fracture and metal loss, make cost-effective run-repair-replace decisions, and solve problems that may arise throughout the lifecycle of a component.
API 579/ASME FFS-1
元素routinely performs the API 579/ASME FFS-1 standard to assess the stability and propagation rates of different types of defects, which can be found in a component both in the design and in service. Our experts are qualified to Level 2 and 3 for NDT and metallographic replicas with specialist knowledge in断裂韧性,finite element analysis [FEA], andfatigue testing.
Our approach
Equipment may contain flaws, become damaged, or aged so that it cannot be evaluated using the original construction codes. API 579-1/ASME FFS1 can be used to assess the equipment for continued operation. It allows:
- Thermo-mechanical analysis under operating conditions (temperature and strain): normal service, transients, predictable exceptional or faulted service conditions.
- Structural analysis under normal operating conditions aimed at the detection of anomalies (thickness reduction due to corrosion/erosion, subsidence/displacement of supports/anchors) to evaluate the further use and the need for any corrective actions
Design, design verification, faulted component assessment, and requalification. - Defects propagation rate evaluation and stability assessment for operating conditions according to recognized procedures and standards (API 579, BS 7910, DNV, NE R5, NE R6).
Evaluation of structural inspection results and assessment of the severity of the detected flaws
Assisting failure analysis investigation and evaluation of the plausibility of a failure scenario
Related services
Element one of the most comprehensive services for the Oil and Gas sector,
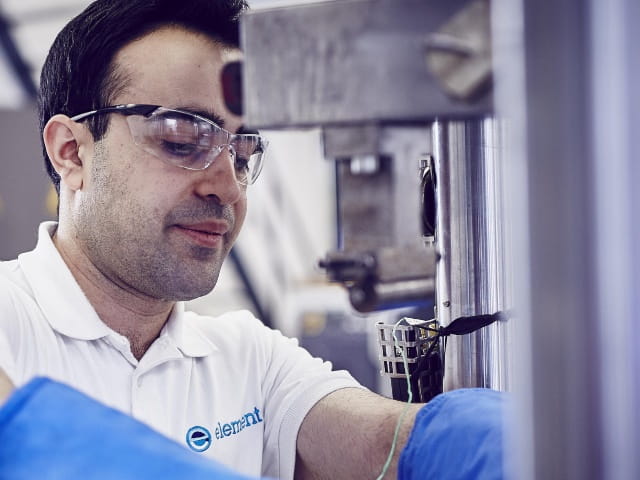
Fracture Toughness Testing
Find out how Element utilizes its fracture toughness testing capabilities and expertise to predict and prevent potential pipeline cracking and failure.
Read More
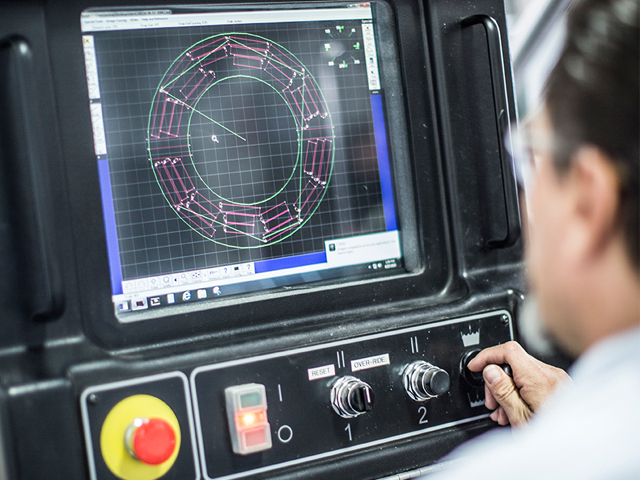
Engineering Critical Assessments
Element's fully integrated engineering critical assessment services are crucial to mitigating failures of pipelines, pressure vessels, offshore platforms, and engineering structures.
read more
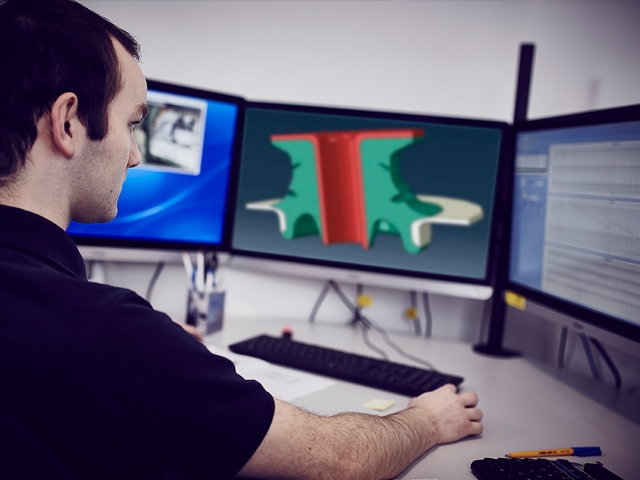
Finite Element Analysis (FEA) Services for Products, Systems & Components
Element offers advanced numerical analysis service using Finite Element Analysis (FEA) techniques using industry standard software to predict the long term behavior of materials components and products when in service.
Read More
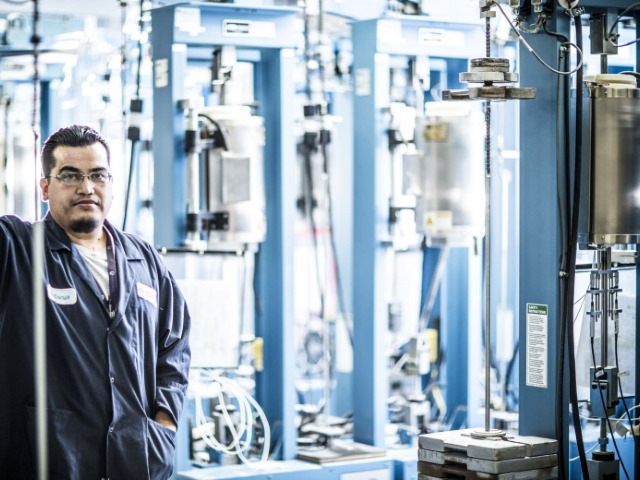
Creep Testing
Measuring load over an extended period of time, creep testing programs use continuous load and elevated temperature to test for eventual material failure.
Read More
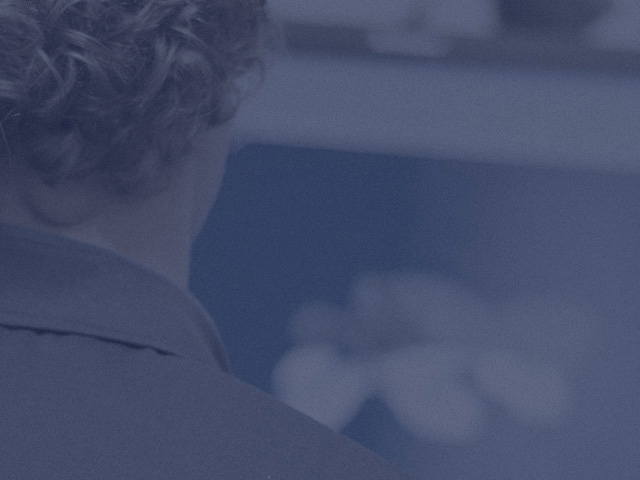